A new order for some advanced Basecamp features came in. I checked the weblog of the client to see where they are coming from and ran into a new term: neo-Taylorism. Taylorism apparently had very negative connotations. My only acquaintance with Taylor is with the sails manufacturer and the association is positive. I decided to go digging and in the process ran into the concepts of:
- scientific management
- human relations movement
- Toyota production system
Running a company is a pain in the neck tremendously challenging.
If you are in the knowledge business, there are two major challenges:
- managing people
- managing process
You are spared the pain of managing inventory. In a sense, time becomes your inventory but it does at least take a third dimension out of the equation, in comparison to auto parts production where you really, really need to manage raw materials and parts.
What’s cool about business theory is that it’s all been invented before.
Scientific Management: neo-Taylorism
This Taylor is Frederick and he died in 1915, before Henry Ford’s factories were built. Frederick Taylor came up with something called Scientific Management. The basic idea was to improve workflow (hey I need some of that) and labour output (work faster!).
The basic idea is that best practice methods should be documented and taught: all workers should produce quality work. A good start. The problem remains that with equal pay, there is no disincentive for workers not to dog it or goldbrick. Taylor called this slow working “soldiering”. Many workers call it “getting through the day”. I’ve got a friend like this. Once someone approaches work like this, that person is nearly unemployable at Foliovision or anywhere else where enthusiasm, productivity and quality of work are valued.
The way we prevent that here is by a bonus system. About 1/5 to 1/2 of any given employee’s income should come in bonus. We’ve run into a bit of a brick wall with one department and a certain group of employees. The basic policy is to pay over market rates so people want to keep working here rather than bouncing. We have great working conditions and a wonderful team, but working here is more stressful than at 80% of Slovak companies as we deal with demanding international clients (yes, that’s probably you).
The problem we are running into with this policy is that some people have decided that the high salary is enough and they just want to do their hours and couldn’t care less about their bonuses.
Taylor’s scientific management has a way to combat that. Quantify the time needed for a certain activity and then pay by piecework. We won’t go that far, but we will set standards for the work and then measure how many items were done, check quality and client complaints and then pay the bonus. The next step is that due to the newfound soldiering (we didn’t have this issue six months ago), we’ll have to reduce base pay in vulnerable departments. We won’t pay those performing with enthusiasm or speed any less than they make now, but those determined to soldier through their days will make less.
The problem with having people soldier is that it’s a contagious attitude and will destroy a company from the inside out. Even a single such team member getting away with it for more than a month will demotivate the rest of the team. I won’t let this happen here.
Human Relations Movement
Now the problem with Taylorism is that while his scientific management weeds out waste and increases productivity, it treats people as draft animals or machines. His theories in practice nearly destroyed Watertown Arsenal and Congress had to step in to ban his methods.
In reaction the Human Relations Movement came along under Hawthorne and George Mayo and advocated more groups more in line with natural human social order take priority over artificial organizational structures and two-way communication from shop-floor to executive offices. Good leadership means goals are clearly communicated once decisions reflecting the collective wisdom are made.
In principal, following HRM practices should reduce discontent among company employees and more harmony in the workplace. Conflict resolution and soft skills are part of HRM. Neo-Taylorism means ignoring HRM, hence the negative connotations of Scientific Management.
Fordism: Scientific Management’s Influence on Henry Ford
Curiously one would think that Taylor’s theories would have had a great influence on Henry Ford and Ford’s invention of the assembly line. It turns out no: Taylor visited the Ford plant in 1914 and was surprised to learn that “had undertaken to install the principles of scientific management without the aid of experts” according to Charles Sorensen.
Scientific Management was an idea whose time was ripe, like a windowed operating system, an app store or 1 click shopping. The idea was invented in multiple places at nearly the same time. Allowing patents to business process is a dangerous route, but we are slipping off topic.
Surely there must be a better way than the resented Taylorism, the diffuse Human Relations Management or the mechanical Fordism. Apparently there is.
TPS: Toyota Production System
TPS is how Toyota became the best car manufacturer in the world. In the quest to systematise their business, Toyota set about integrating Scientific Management with HRM and Fordism.
The quest is to reduce waste. Waste occurs by over production or unnecessary motion or waiting. Overstock is also another kind of waste (same problem with hours in knowledge work). When visiting Detroit in the 1950’s, senior Toyota management were not impressed with all the excess inventory at the Ford auto plants. They were more impressed with how an American supermarket kept track of all stock sold and at the end of every day reordered what had been sold. Toyota took basic supermarket order systems and developed just-in-inventory for advanced industrial production.
Here are the current Toyota Way principles for my reference:
Continous Improvement
- Challenge (We form a long-term vision, meeting challenges with courage and creativity to realize our dreams.)
- Kaizen (We improve our business operations continuously, always driving for innovation and evolution.)
- Genchi Genbutsu (Go to the source to find the facts to make correct decisions.)
Respect for People
- Respect (We respect others, make every effort to understand each other, take responsibility and do our best to build mutual trust.)
- Teamwork (We stimulate personal and professional growth, share the opportunities of development and maximize individual and team performance.)
Some additional components of The Toyota Way
Long-term philosophy
Base your management decisions on a long-term philosophy, even at the expense of short-term financial goals.
The right process will produce the right results
- Create continuous process flow to bring problems to the surface
- Use the “pull” system to avoid overproduction
- Level out the workload (heijunka). (Work like the tortoise, not the hare.)
- Build a culture of stopping to fix problems, to get quality right from the first
- Standardized tasks are the foundation for continuous improvement and employee empowerment
- Use visual control so no problems are hidden
- Use only reliable, thoroughly tested technology that serves your people and processes.
Add value to the organization by developing your people and partners
- Grow leaders who thoroughly understand the work, live the philosophy, and teach it to others.
- Develop exceptional people and teams who follow your company’s philosophy.
- Respect your extended network of partners and suppliers by challenging them and helping them improve.
Continuously solving root problems drives organizational learning
- Go and see for yourself to thoroughly understand the situation (Genchi Genbutsu, 現地現物);
- Make decisions slowly by consensus, thoroughly considering all options (Nemawashi, 根回し); implement decisions rapidly;
- Become a learning organization through relentless reflection (Hansei, 反省) and continuous improvement (Kaizen, 改善).
So it is possible to reconcile neo-Taylorism, the Human Relations Movement, Fordism and create a very successful company.
More importantly, you can treat people well, help them fully develop their potential, all in a rigorously disciplined environment. Creative anarchy is not necessary for more of the process of making great websites and probably not even for the creation of great content.
As I mentioned above, in knowledge work there is very little physical inventory. One has tools like computers and software but those tools are more like the machines in an automobile plant than production inventory.
In knowledge work or a service business, one’s inventory are the staff hours.
One element which we successfully use at Foliovision to decrease waste hours is constant over-demand. I carefully take on just enough work to make sure we are never wondering what to do next and never overstaff. There is nothing more deadly to productivity than having too little to do. We have to skirt a tight line though in too much work and too little.
Too much work is depressing for all involved and will inevitably result in either lateness and/or a slip in quality. Too little work results in slow work and reduced paycheques (we work on a bonus system) and a slip in morale.
Stay tuned for part two about how Apple Computer handles workload.
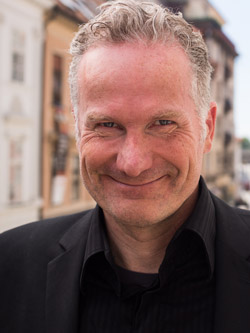
Alec Kinnear
Alec has been helping businesses succeed online since 2000. Alec is an SEM expert with a background in advertising, as a former Head of Television for Grey Moscow and Senior Television Producer for Bates, Saatchi and Saatchi Russia.
Leave a Reply